Machine learning in a critical production system
The VELUX Group enter the future with machine learning to optimize the capacity of production
With a well-defined goal to increase the capacity and quality of a critical production line, the VELUX Group and kaastrup|andersen have collaborated on developing a first take on an analysis of sensor and production data that has resulted in a prototype of a machine learning model. The model provides experience-based predictions of the optimal adjustments in the production equipment when circumstances (for example, change of material in production) require it.

"kaastrup|andersen helps us see the benefits of using machine learning in production - a tool that can make our production more efficient and easier to manage."
Challenge
The VELUX Group always focuses on how production can be most efficient, among other things by using new methods to process data from production machines. One of the VELUX Group's key production lines had the potential to be more efficient: A considerable amount of material is scrapped when changing aluminum coils, and time was also wasted. The goal was to increase the capacity and avoid bottlenecks in the critical production process by utilizing available data.
The VELUX Group worked with kaastrup|andersen to explore the possibilities of using machine learning to optimize the production line and at the same time to try new ways of analyzing performance, efficiency and potential.
Solution
Data from different points in the production process was picked up via a number of sensors in the production machines. At the same time, more general production data was collected, and the large amount of diverse data formed the basis for a thorough analysis. The actual analysis work was performed by using tools that uncover correlations, peak loads, links and patterns that can form the basis of machine learning models. In this context, well-founded and successful machine learning will mean that the production system is constantly 'getting smarter' on how processes need to be adapted to optimize performance.
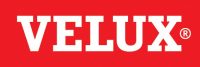
Result
The analysis of the collected data showed clear correlations between different parts of the production process. The results formed the basis for a simple machine learning model that predicts which parameters need to be adjusted as the elements in the production change, based on experience. The model can be extended to provide the production line operator clear instructions on what needs to be adjusted in each situation.
The first analysis clearly shows that applying machine learning in the production line holds great potential, and the VELUX Group and kaastrup|andersen are looking at the next phase of the project, where dynamic extraction of real-time data from the sensors in the equipment is being worked on. The goal is to achieve a process that regulates deviations (e.g. caused by temperature fluctuations, variable filling in profiles, etc.), so that in the long term it is possible to reduce the high requirements for operator competencies. To achieve the goal, a more comprehensive machine learning model is developed, which incorporates even more parameters and can provide more detailed, up to date and concrete feedback.
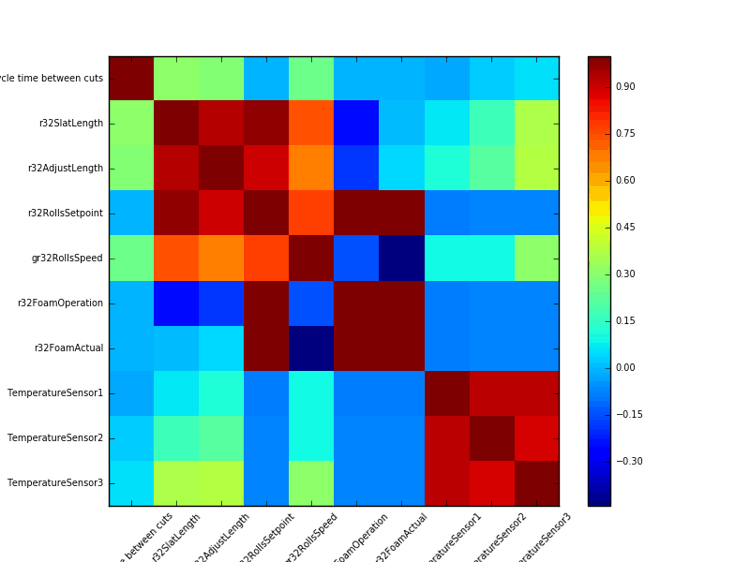